Standred & Specification
PROPERTIES OF UPVC PIPES:
The physical, chemical and mechanical properties of Vigor pipes and Otting demonstrate their superiority in utility and applications over conventional system
DENSITY
The density of Vigor pipes is approximately 1.43g/cm3, which is almost 1/6th the weight of cast iron and steel, thus making it much cheaper to transport and easier to handle during installation.
MECHANICAL STRENGTH
Vigor CPVC Pipes are suitable even in varying conditions, because of its mechanical strength. This can be gauged from the fact that the tensile. Dexural and compressive strength of CPVC is around 450 kg/cm2
HYGIENIC
Vigor CPVC Pipes offer the most hygienic means of Quid transportation. They are highly capable in fighting attacks by fungi and are not subject to contamination. The inside surface which is extremely smooth, does not support any growth. encrustation or fuming, and no odor or taste is transmitted to the Quid being conveyed. This property is of prime importance for the transportation of potable water to towns and villages.
CHEMICAL RESISTANCE
Vigor CPVC Pipes is unaffected by most concentrations of acids, alkalis, organic chemicals, oils and fats. This resistance to corrosion by most chemicals akes vigor CPVC pipes indispensable for contemporary industrial applications and for sewerage purposes
FLEXIBILITY
Being a thermoplastic material, Vigor CPVC is more capable to withstand deformation due to earth movements. Vigor CPVC pipes in this respect are considerably more popular than metallic and asbestos cement pipes, which can collapse under stress levels
FIRE RESISTANCE
Vigor CPVC pipes do not support combustion and are self-extinguishing, a fact that has been proven over a considerable amount of time. They are, therefore. ideally suited for use in buildings and other constructions.
DIMENSIONS OF Vigor CPVC pipes
Vigor CPVC pipes are manufactured conforming to the latest stringent Indian and American standard
Note: Vigor CPVC pipes means unplasticised polyinylchloride pipe, also frequently referred to as rigid PVC pipe. The word rigid does not explain its structure, but denes a property, which is self explanatory.
Installation Guide
Easy and 100% leakproof installation.
Step 1: Cutting
Measure the pipe length accurately and make a visible marking using a felt tip pen. Ensure that the pipe and fittings are size compatible. You can easily cut with a plywood cutting saw/ ratchet cutter or a wheel cutter. Cutting the pipe as squarely as possible (at 90°) provides optimal bonding area within a joint. Inspect pipe ends thoroughly prior to making a joint. If a crack or splintering is noticed cut-off a minimum of 25 mm beyond the visible crack before proceeding.
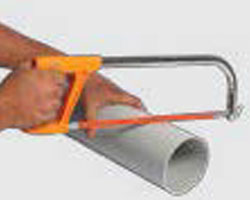
Step 2: Deburring/Beveling
Burrs in and on pipe end can obstruct flow/proper contact between the pipe and socket of the fitting during assembly and should be removed from both in and outside of the pipe. A 15 mm dia half round file/a pen knife or a deburring tool are suitable for this purpose. A slight bevel on the end of the pipe will ease entry of the pipe into the socket of the fitting socket.
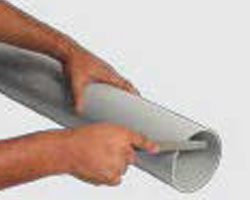
Step 4: Fitting Preparation
Using a clean dry rag, wipe the dirt and moisture from the fitting sockets and pipe end. Dry fit the pipe to ensure total entry into the bottom of the fittings socket and make a visible marking using a felt tip pen.
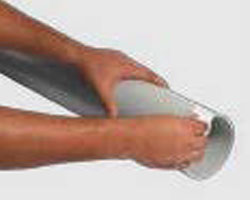
Step 5: One Step Solvent Cement Procedure
Use only Ashirvad FLOWGUARD PLUS™ CPVC Solvent cement conforming to ASTM F-493 to ensure a perfect solvent weld Joint. When making a joint, apply an even coat of solvent cement at the end of the pipe and also inside the fitting socket. Do not use thickened or lumpy solvent cement. It should have a flow consistency like that of syrup or paint.
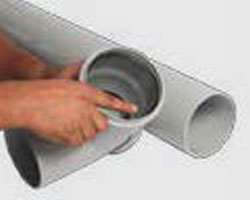
Step 5: Assembly
Immediately insert the pipe into the fitting socket, rotate the pipe 1/4 to 1/2 turn while inserting. This motion ensures an even distribution of solvent cement within the joint. Properly align the fittings as per patented alignment system shown with picture diagram on the right side. Hold the assembly for 30 seconds to allow the joint to setup and avoid push-out.
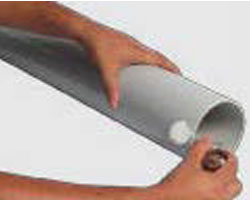