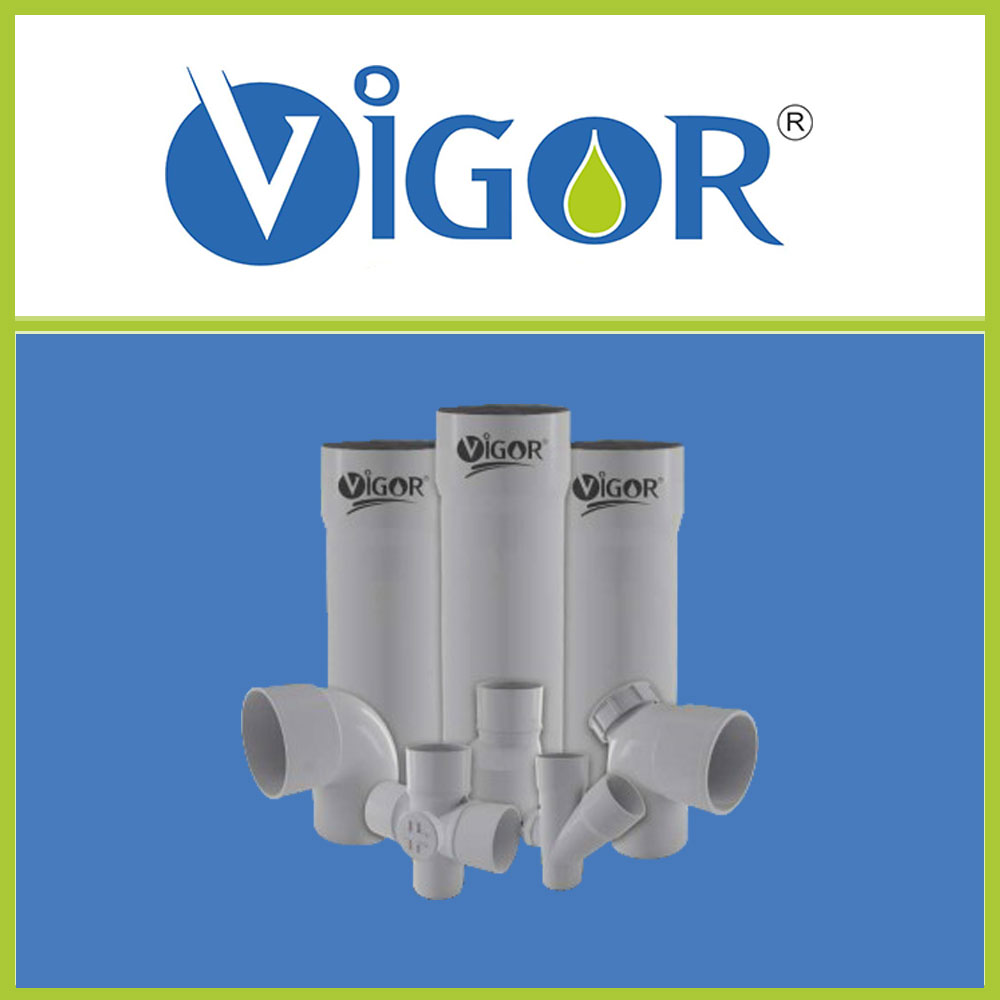
SWR Sel fit fittings
- Non Corrosive
- Resistance To chemical
- Thogh & Reliable
- Easy Cold Welding Process
- Prevent Bacterial Growth
- Low Thermal Expansion
- Life off More than 50 Years
- For Sewage Waste & Rain Water
SWR SELFIT PIPES AS PER : 13592, SWR SELFIT FITTING As PER IS : 14735
Fittings
Standard & Specification
PROPERTIES OF SWR SEL FIT FITTING:
Vigor SWR (Soil, Waste, and Rainwater) Sel fit fittings are designed to meet the specific requirements of drainage systems in buildings. While precise details may vary depending on the manufacturer's specifications, here are some general properties associated with Vigor SWR Sel fit fittings:
High-Quality uPVC Material:
Vigor SWR Sel fit fittings are typically constructed from high-quality unplasticized polyvinyl chloride (uPVC), ensuring durability and longevity in drainage applications.
Corrosion Resistance:
These fittings offer excellent resistance to corrosion from chemicals, acids, and alkalis commonly found in sewage and drainage systems, ensuring long-term reliability.
Leak-Proof Seals:
Vigor SWR Sel fit fittings are designed with precision-engineered seals and joints, ensuring leak-proof connections and preventing the escape of wastewater or gases.
Easy Installation:
These fittings are designed for easy and efficient installation, allowing for quick assembly and reducing labor costs during construction or renovation projects.
Compatibility:
Vigor SWR Sel fit fittings are typically compatible with uPVC pipes of the corresponding size and pressure rating, providing flexibility in system design and installation.
Temperature Resistance:
They exhibit high temperature resistance, allowing for use in applications where elevated temperatures may be encountered, such as hot water drainage systems.
Impact Resistance:
These fittings are resistant to impact and mechanical stress, reducing the risk of damage during handling, transportation, and installation
Dimensional Accuracy:
Vigor SWR Sel fit fittings are manufactured to precise dimensional tolerances, ensuring proper fitment and alignment within the drainage system.
Note: Vigor CPVC pipes means unplasticised polyinylchloride pipe, also frequently referred to as rigid PVC pipe. The word rigid does not explain its structure, but denes a property, which is self explanatory.
Installation Guide
Easy and 100% leakproof installation.
Step 1: Cutting
Measure the pipe length accurately and make a visible marking using a felt tip pen. Ensure that the pipe and fittings are size compatible. You can easily cut with a plywood cutting saw/ ratchet cutter or a wheel cutter. Cutting the pipe as squarely as possible (at 90°) provides optimal bonding area within a joint. Inspect pipe ends thoroughly prior to making a joint. If a crack or splintering is noticed cut-off a minimum of 25 mm beyond the visible crack before proceeding.
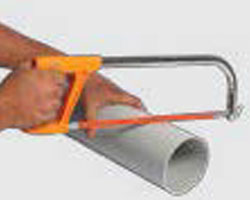
Step 2: Deburring/Beveling
Burrs in and on pipe end can obstruct flow/proper contact between the pipe and socket of the fitting during assembly and should be removed from both in and outside of the pipe. A 15 mm dia half round file/a pen knife or a deburring tool are suitable for this purpose. A slight bevel on the end of the pipe will ease entry of the pipe into the socket of the fitting socket.
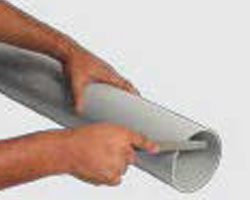
Step 4: Fitting Preparation
Using a clean dry rag, wipe the dirt and moisture from the fitting sockets and pipe end. Dry fit the pipe to ensure total entry into the bottom of the fittings socket and make a visible marking using a felt tip pen.
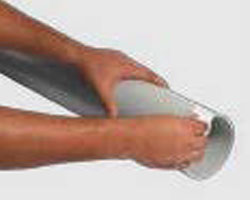
Step 5: One Step Solvent Cement Procedure
Use only Ashirvad FLOWGUARD PLUS™ CPVC Solvent cement conforming to ASTM F-493 to ensure a perfect solvent weld Joint. When making a joint, apply an even coat of solvent cement at the end of the pipe and also inside the fitting socket. Do not use thickened or lumpy solvent cement. It should have a flow consistency like that of syrup or paint.
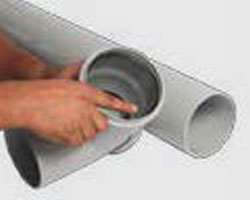
Step 5: Assembly
Immediately insert the pipe into the fitting socket, rotate the pipe 1/4 to 1/2 turn while inserting. This motion ensures an even distribution of solvent cement within the joint. Properly align the fittings as per patented alignment system shown with picture diagram on the right side. Hold the assembly for 30 seconds to allow the joint to setup and avoid push-out.
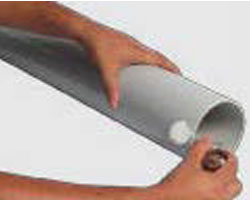